Case Study: Mixing Starch into Dextrose Processing Using Eductors
OVERVIEW
Dextrose is the sugar molecule that is the foundation in almost everything we consume, from sweeteners, to organic acids, and even medicine. It can also be used for fuel in ethanol. Bi-products from dextrose are also added in biofuels and other sustainable fuels to reduce carbon footprint. According to the USDA, dextrose production has increased since 2020 and will continue to increase in production in 2024.
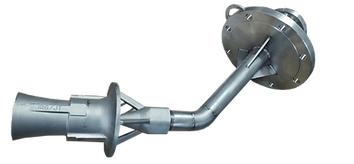
The production of dextrose has two main processes: reaction and filtration. Dextrose is derived from starches within corn and soybeans along with cellulose from vegetation. This raw material is pumped into large tanks where an enzyme is added. This is constantly mixed at 145 deg F to allow the starches to be extracted from the raw material. Mixing efficiency is required to ensure everything within the tank is converted within a reasonable amount of time. In-tank eductors are used for mixing and are strategically angled and placed within the tank to ensure flow fields drive the velocity profiles within the tank above the minimum required valves for an efficient reaction with the enzymes. The reacted starch is filtered to separate dextrose and unwanted solids.


In-tank eductors are preferred for this mixing application due to their low shear, which will mix the tank contents without breaking down the dextrose, a common occurrence with other forms of mixing, like mechanical agitators. Mechanical agitators also tend to focus in a single direction and cannot be optimized to support unique tank geometry or process variations. In-tank eductors are piped in via a header system that is connected to the recirculation pump. The eductors are strategically placed along this header system pointing in different directions to ensure the entire tank has movement.
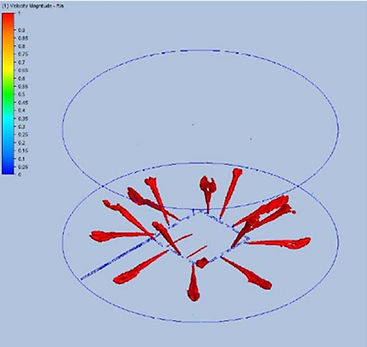
COMPUTATIONAL FLUID DYNAMICS (CFD)
To ensure mixing efficiency, CFD (computational fluid dynamics) can be used to model the tank and mimic flow within the tank where the flow parameters are input into the software. The model breaks down velocities within the tank at various spots at various times. The model also shows the recommended placement, quantity, and angle of the eductors along the header system. The CFD example below shows a tank for a dextrose processing plant that shows the eductor placement and the velocities.
A dextrose production company in the Midwest has recently received our eductor header system for their tanks and is currently running with no issues. They are meeting or exceeding production goals and are pleased that they have had a smooth transition to the new technology without a step back in production. Also there are no solids build up to report of, which is exactly what the eductors were to designed to do.
Fill out the form below to request more information on in-line or in-tank eductors or to discuss your application with our eductor technical expert.
CONCLUSION
In conclusion, tank liquid agitators are a great method of blending, moving liquid, reacting, and keeping temperature unified for dextrose production. The equipment provides low sheer while maintaining the necessary velocities within the tank to maximize process efficiency. They reduced cost in maintenance by having no moving parts in contact with the process and they help reduce waste and unwanted solids in the tank.